How Toyota builds cars – and what it teaches other companies
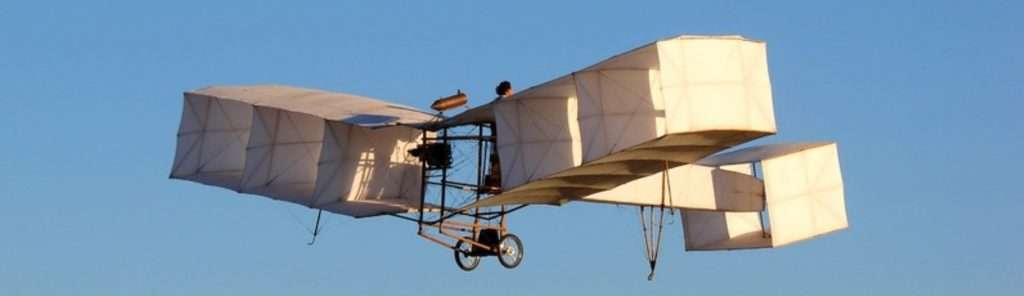
Bombardier Inc.’s Toronto plant employs an efficiency system developed by Toyota Motor Corp.
At first blush, the operations Simon Roberts and Dr. Kevin Smith could not be more different. Mr. Roberts oversees the construction of some of the most complex aircraft in the world as head of Bombardier Inc.’ s Toronto plant in Downsview; while Dr. Smith is tasked with overseeing St. Joseph’s Healthcare in Hamilton as its chief executive.
But upon closer examination, a number of similarities between the two emerge, and in particular the challenges they face on a day-to-day basis. Both are in charge of huge facilities with a highly skilled workforce while trying to manage an extremely complex and precious product.
The goal for Mr. Roberts is saving money in an extremely high-cost, low-margin business. For Dr. Smith, it’s about saving lives.
They have also both turned to a somewhat unusual source recently to help them run their operations more efficiently: Toyota Motor Corp.
The Japanese automaker has long been considered the gold standard in lean manufacturing. But in recent years, other industries outside of the auto sector have also begun to adapt Toyota’s methods to streamline and improve upon their own operations, including both Bombardier and St. Joe’s in recent months.
The “Toyota Production System” was developed in the 1950s at a time when the Japanese auto industry was suffering, and Toyota, in particular, lacked the cash it needed to fund its operations and or even keep enough inventory on hand to build its cars.
In an effort to improve its operations, Toyota’s founders travelled to the United States to see how the wildly successful system instituted by Henry Ford built cars. But they were said to be less impressed by Ford’s plants than a system being used at the local grocery store: an automatic drink resupplier, where a customer wants a drink, takes one, and then another one replaces it. It was this machine, and its ability to hold only the inventory needed, that is credited with planting the first seed for what would eventually develop into the “Toyota Way” of building cars.
In order to implement real change in today’s organisations it is critically important to first establish compelling reasons why it is impossible to continue without change. A base axiom of the Gestalt school of psychology is that people will remain in the same place until it becomes too uncomfortable to remain there.
From a global perspective, the emergence of the German and Japanese industry can be traced to the immediate post-WWII period. Indeed, a noted Japanese industrialist, when questioned in Australia about how Australian business could become world-class, advised that it should not even try – with the climate, quality of life and relative economic success they enjoy, Australians would never be in the absolute “backs to the wall” situation of Japan and Germany in the late 40s and early 50s. He recognised the importance of the burning platform – jump and maybe die or stay and certainly die. As we have seen with recent global events and particularly the impact of covid, fear, while an extremely negative emotion is a powerful motivator.
Western industrial history since the 1960s is littered with examples where leaders either failed to recognise, or at least were unable to get their companies to recognise, that a burning platform was present. The result was the slow, painful death of key industries. Part of this reason for lack of recognition is the very slow burning of the platform – from the initial spark to the death of an industry takes upwards of 10 years.
For many industries the platform is well and truly burnt, the companies involved now merely ghosts and the painful memories of their decline a distant recollection. But for many more, the platform has only recently begun to warm up. Like the proverbial frog in a saucepan of water, if the temperature rises only slowly it is much more difficult to recognise and react appropriately, than if dropped suddenly into boiling water. It is this insidious, creeping threat that industries have failed to understand until too late.
Responses